DBM Full Form in Road Construction:
The Dense Bituminous Macadam (DBM) mix shall be prepared in a Hot Mix Plant (HMP) as per the approved Mix Design, complying with clauses 507.2 and 507.3 of MORTH. The HMP shall have at least four cold bins, a four-deck vibratory screen, and hot bins to store the heated aggregates. Precautions shall be taken to control the entrance of moisture.
Also, Read: Dense Bituminous Macadam (DBM) Construction Requirements
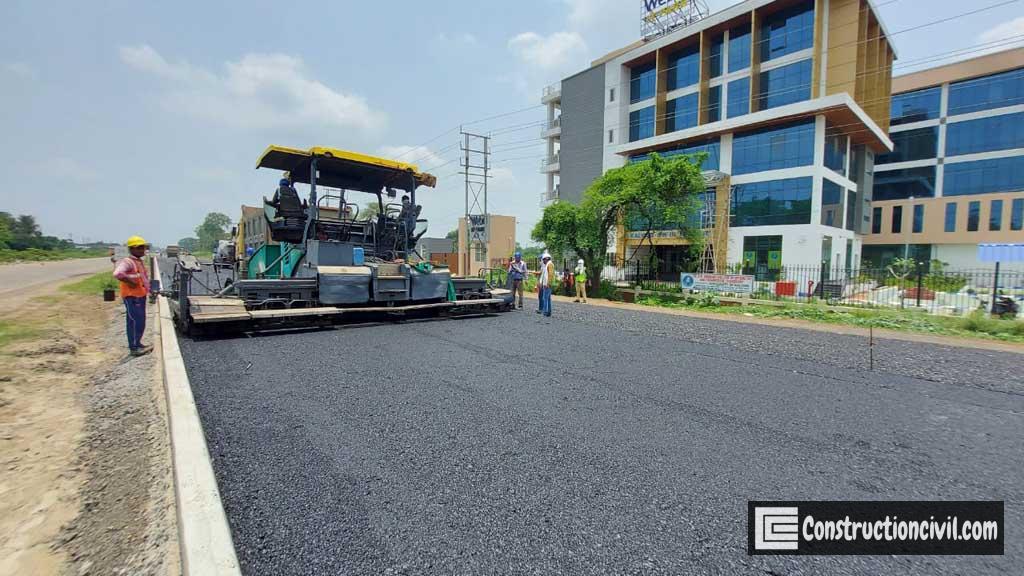
Also, Read: Prime Coat and Tack Coat using Cationic Bitumen Emulsion for Road Work
Preparation of Dense Bituminous Macadam (DBM)ย Mix and Transportation:
The mixing plant shall be of batch-mix type. It shall be capable of regulating the composition of the mixture to within the tolerances as specified in table 501.3 of MORTH concerning the approved job mix formula.
- The rated capacity of the DBM mixing plant shall be 200 T/hr.
- The storage Bitumen tanks shall be capable of maintaining their contents at the specified temperature within a tolerance of ยฑ5ยฐC. They shall be equipped with a thermostat to prevent temperatures from rising above 170ยฐC, and a fixed thermometer quickly read from outside the tank.
- The dryer shall be of rotating drum type capable of heating the aggregates to the temperatures outlined in the specification.
- Bitumen shall be heated to the specified temperature in the tanks and delivered to the mixing plant via insulated pipes to minimise heat losses.
- The minimum mixing period shall be adopted to get an appropriate mix. The mixing cycle times shall be in the range of 30 to 40 seconds.
- HMP shall have automatic controls that coordinate the mixer proportioning, timing and discharge.
- The Bitumen shall be heated in the range of 150ยฐC to 165ยฐC as it can be distributed uniformly.
- The Aggregates shall be heated to mix within the temperature range of 150ยฐC to 170ยฐC. The difference in temperature between the binder and the aggregate does not exceed 14ยฐC.
- The mixing shall be thorough to ensure that a homogeneous mixture is obtained.
- Discharge temperature of dense bituminous macadam mix shall be 165ยฐC maximum.
- Bituminous Mixes shall be kept free of contamination and segregation during transportation.ย
- Dumpers used for the hauling of Asphalt mixture shall be adequately free of petroleum oils, solvents, or other materials that adversely affect the Asphalt mixture.ย
- The Dumpers shall be covered with tarpaulins while carrying the mix to the site.

Also, Read: Granular Sub Base Construction and Quality Control
Laying of DBM In Road Construction:
- The Dense Bituminous Macadam (DBM) materials shall be laid by a self-propelled sensor paver finisher equipped with a hopper and delivery augers capable of spreading, tamping and finishing the mix to specified grade, lines and cross-section.ย
- It shall be able to lay bituminous materials with no segregation, burning, dragging or other defects and within the defined level and surface regularity tolerances and shall satisfy the specification as per clause 507.6 of MORTH.
- Immediately after receiving the transported materials from the Hot Mix Plant at the site, it shall be spread on the prepared and approved surface.
- The dense bituminous macadam mix shall be spread to line and level by the sensor paver without segregation, tearing or dragging.ย
- The dense bituminous macadam mix temperature at the time of laying shall not be less than 120ยฐC.
- The dense bituminous macadam mix shall be placed at the full width of the pavement.
- The compacted thickness of any dense bituminous macadam layer shall be as per the specification.
- The paver shall be capable of working at forwarding speeds compatible with uniform and continuous laying of the dense bituminous macadam mix.ย
- The condition shall be seen to avoid a continual stop-and-start fashion.ย
- The speed of the sensor paver shall be coordinated with the feed speed limiting to no drag condition.
- The paver shall be equipped with accurate screed controls for maintaining the screed at the specified longitudinal grade and transverse slope.ย
- The operation shall be capable of maintaining the screed at the specified transverse slope within the allowable tolerance.
- Automatic controls in the paver shall be backed by manual controls that can be optionally activated, in case required.
If the automatic controls fail or malfunction, the equipment shall be operated manually for the remaining job, provided that the specified requirements are to be fulfilled.

Also, Read: Concrete Subbase Course – DLC Construction
Compaction of the Dense Bituminous Macadam:
Sufficient rollers of appropriate types, sizes and weights shall be provided to achieve the specified compaction. Rollers shall be of self-propelled and of steel wheel, pneumatic tyre and vibratory types, including combinations thereof, capable of reversing without shoving or tearing the mix.
- The laid dense bituminous macadam mix shall be rolled, and rolling shall be finished before the mix temperature attains below 100ยฐC, minimum.
- Rolling shall continue as far as possible after laying the mix so that the mixture is neither too workable such that rolling causes undue displacement or shoving nor too stiff, offering resistance to the desired degree of compaction.
- Initial or breakdown rolling shall be done with 8-10 tonnes of static tandem Rollers.ย
- The rollers shall be worked with the drive roll nearest to the laying equipment at a uniform speed not exceeding 5 km/hr.
- Intermediate rolling shall follow immediately upon initial rolling with an 8- 10 tonnes deadweight vibratory roller.
- It shall be followed by intermediate rolling with a pneumatic tyred roller of 12-15 tones weight having a minimum tyre pressure of 5.6 kg/sq cm.
- The finish rolling shall be done with an 8-10 tones static Tandem roller to eliminate marks of the previous rolling.
- Initial rolling -2 static passes with Vibratory roller.
- Intermediate rolling – 2 vibratory passes with a Vibratory roller.
- Final rolling -2 passes with Pneumatic Tyred Roller (PTR).
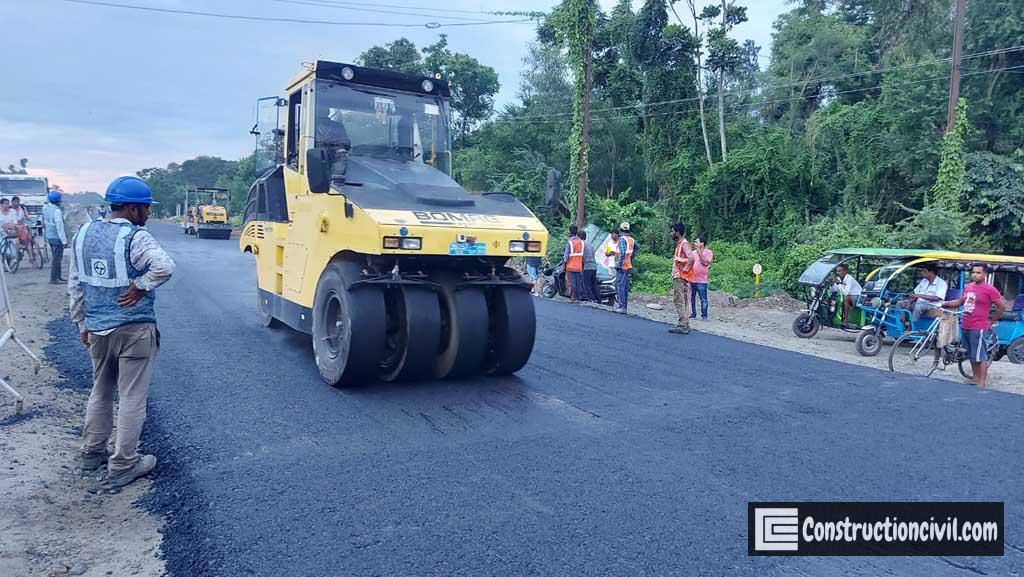
Also, Read: Wet Mix Macadam Construction and Quality Control
- The roller wheels and drums shall be kept lightly moistened with water to prevent the adhesion of the mixture to the rollers.ย
- Rolling shall start from the outer edge and move longitudinally parallel to the centerline, each pass overlapping the previous pass by one-third of the roller width.ย
- On super elevated portions, rolling shall begin at the low side and progress towards the high side. Rolling shall be continued till the air voids and density.
Also, Read: What is Road Kerb – Types & Construction Methodology
Finishing of Edges after Bituminous Macadam Laying:
- Any dense bituminous macadam mix that becomes loose or broken, mixed with dirt or foreign matter, or defective shall be withdrawn and shall be replaced with a new hot mix and compacted.
- The edges of the DBM course shall be rolled concurrently with or shortly after the finishing.ย
- For edges, roller wheels shall extend 50.00 mm to 100.00 mm beyond the edge.ย
- Any fresh dense bituminous macadam mix on the existing work shall be removed carefully, sweeping it back onto uncompacted work to avoid irregularity formation on the previous surface.
Surface Finish and Quality Control of DBM:
The surface finish of construction shall conform to the requirements specified in clause 902 of MORTH, and all materials and workmanship shall comply with the requirements mentioned in section 900 of MORTH. The finished level of DBM shall be within the tolerance limits specified in Table 900.1. (i.e. +6 mm to โ 6mm).
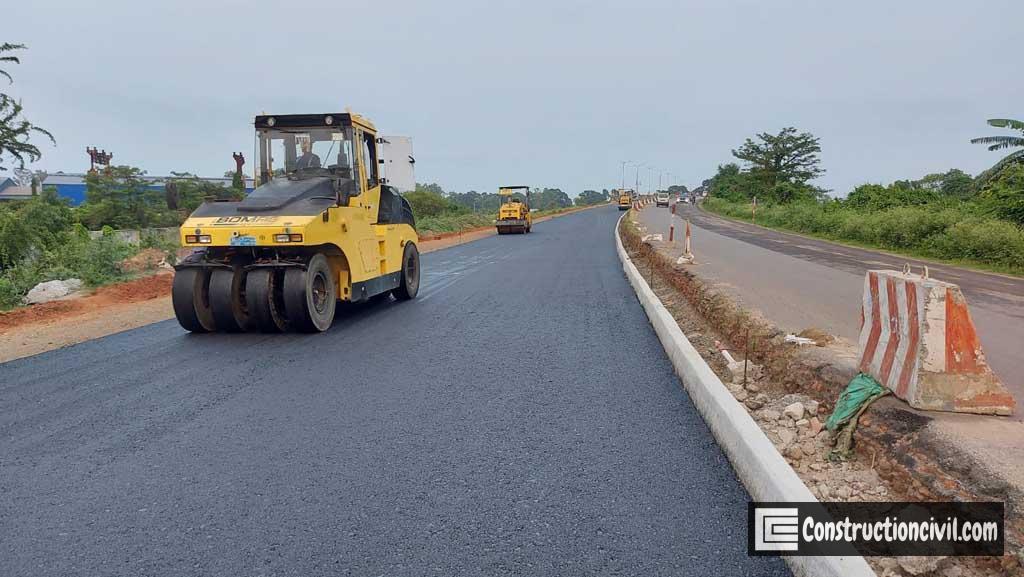
Arrangement for Traffic Flow after DBM:
During the construction period, arrangements for traffic flow shall be made as per clause 112 of the MORTH technical specification.
Limitations to DBM Construction:
- Laying shall be suspended while free-standing water is present on the surface. * Surface should be covered during rain, fog and dust storms, if possible.
- After the rain, the bituminous surface, or surface coated with prime or tack coat, shall be blown off with a high-pressure air jet to remove excess moisture, or the surface shall be left to dry before laying. * Laying of DBM mix shall not be carried out when the air temperature at the surface on which it is to be laid is below 100ยฐC.
- DBM laying shall not be permitted when wind speed at any temperature exceeds 40 km/hr at 2m height unless specifically approved by the SC.
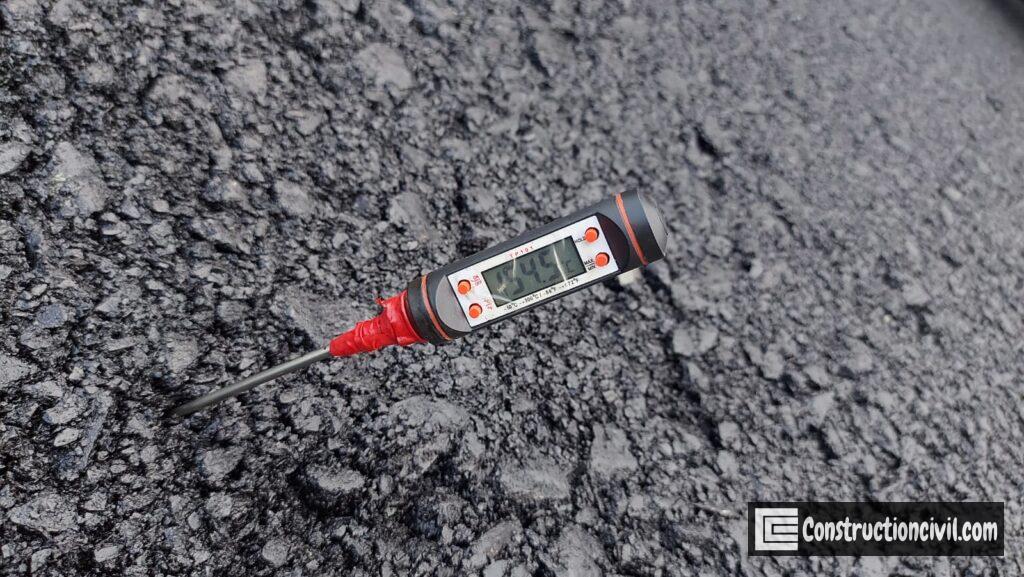
Quality Control Tests for DBM:
- The Quality control tests shall be conducted on the material at the source before transportation to the DBM location.
- After completion of the compaction operation following tests are pertinent to DBM.
SL NO | TEST | CODE | FREQUENCY |
Quality of binder | IS: 73 | Penetration between 60 and 70 | |
Aggregate Impact Value | IS: 2386(part 4) | 30% Maximum | |
Flakiness and Elongation Index | IS: 2386(part 1) | 30% Maximum | |
Stripping value | AASHTO T 182 | Minimum Retained coating 95% | |
Water absorption of aggregate | IS: 2386(part 3) | 2% Maximum | |
sand equivalent test | IS: 2720(Part-37) | Not less than 50 | |
Mix grading | Table 500.9 of specification clause 507 | 1 test for each 400 tonnes of mix subject to a minimum of 2 tests per day | |
Stability of Mix | ASTM D-1559 | 1set of 3 Marshal specimens to be tested for stability, flow, voids every 400 tonnes of mix, subject to a minimum of 2 sets per day. | |
Control of temperature | At regular close intervals | ||
Control of binder content and gradation in the mix | 1 test for each 400 tonnes of mix subject to a minimum of 2 tests per day | ||
Rate of spread of mixed material | Regular control and through checks on the weight of mix and layer thickness | ||
Density of compacted layer | 1 test per 250 Sq.m area |
Also, Read: Asphalt Concrete/Bituminous Concrete(BC) Construction Guide

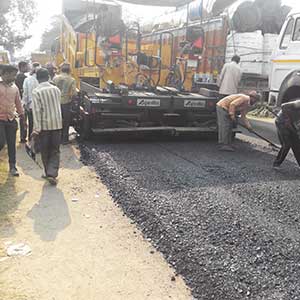
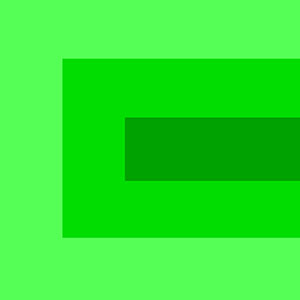
Hi bro..im studying third year civilโฆNow im Design my dream in autocad and staad pro..on the process im lacking in estimateโฆhere that lack of process also cleared thank u so much sir..keep doing bro
This is one of the best blogs for civil engineering students to brush up their subject knowledge and learn new things.
Amazing knowledge share about road,which is help all civil engineer work in the field side.
Thanks for your sharing knowledge.
Hello WhiteHelmet,
My name is Ramtanu, and I’m a Highway Engineer. Thank you for
– important information
– easy to understand
– good for interview
– very clean
Thanks
Wonderful article. Thank Construction Civil
Dear sir,
Very good and quality article for bituminous work. Thank you so much
what effect when mixing, laying & rolling temperature is low